Modular and prefabricated construction methods are becoming increasingly important on senior living projects to address a range of construction challenges such as schedule delays, supply chain issues, skilled labor shortages, and weather impacts.
That was the message from speakers Tracy Lauer, market leader, and Ellen Rath, senior project manager at Cuningham, during their session “Embracing Off-Site Construction Approaches to Deliver High-Quality Solutions,” at the 2025 Environments for Aging Conference + Expo in Lexington, Ky., April 26-29.
Benefits of prefabrication on project timelines
During their session, Lauer and Rath shared two projects from other sectors, including Banner Health’s new hospital tower expansion in Mesa, Ariz., and The Eddi Apartments in Edina, Minn., to illustrate the possibilities for senior living projects.
Prefabrication approaches include panelized construction (prefabricated walls built off-site), components (such as flooring, roofing, or corridor racks), pods (fully finished spaces like bathrooms or kitchens, which are installed into structures), and modules (structural units that are fully built and stackable, although limited by shipping constraints).
Lauer, who led the design of Banner Health’s 5-story vertical expansion, discussed how prefabrication was critical in helping the project to realize faster speed to market, alleviate limited labor supply, and mitigate challenges and impacts to the operational campus.
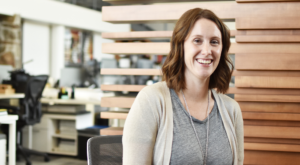
Tracy Lauer (Headshot credit: Courtesy of Cuningham)
“Banner Desert was facing market competition for women’s services as another healthcare system was in the process of completing a new women’s tower in the east valley and didn’t want to lose market share in the women’s services sector,” Lauer said. “How could [Banner] build this expansion as fast as possible, while also addressing labor shortages and disruptions to the active campus? That was a driving factor for prefabrication.”
Specifically, panelized, component, and pod prefabrication were used on the expansion, including 138 exterior panels that were manufactured, shipped to the site, and installed in 30 working days over a three-month period. Comparatively, traditional construction, with scaffolding and multiple trades stacking, would have taken between six to eight months, Lauer said.
Supporting procurement, product consistency demands
Other building elements, such as prefabricated toilet pods constructed in a factory instead of custom built in the field, can be more precisely manufactured, reducing common field issues with floor slopes and tile installation, which many senior living projects face.
“These prefabricated elements can be strategically applied to a variety of senior living projects to similarly increase speed to market, deal with local labor shortages, and provide quality and consistency to projects,” Lauer told attendees.
Additionally, by relocating substantial construction off-site, facilities can reduce noise, dust, and construction traffic—factors especially important in senior living environments housing potentially vulnerable or health-sensitive senior residents.
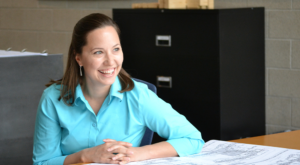
Ellen Rath (Headshot credit: Courtesy of Cuningham)
To ensure a seamless design and construction process for The Eddi, a 202-unit multifamily rental community, Rath said that Cuningham adopted an “inside-out” design strategy, finalizing the units’ interiors early in the project timeline.
“This approach enabled the identification of long-lead procurement items and facilitated concurrent construction efforts: while modules were fabricated in a climate-controlled facility, the on-site team simultaneously built the precast concrete podium,” said Rath. “This level of parallel progress cut the Eddi’s construction timeline by approximately one year compared to similar traditionally built projects—even through Minnesota’s harsh winter.”
Applying modular construction in senior living
Beyond speed and efficiency, the modular method delivered key benefits, including enhanced construction quality, superior acoustic separation between units, and significant waste reduction due to factory-controlled processes—attributes that align directly with the needs of senior living developments, the speakers noted.
Lauer and Rath also stressed that early integration of prefabrication contractors is critical to support implementation on a project.
“Because these processes require early authorization of construction funds in order to meet the shorter construction duration, having all partners onboard and aligned upfront is paramount.” Rath said. “Designers, contractors, and owners have to be aware that long lead items need to be ordered prior to the documents being completed.”
For more coverage of the 2025 EFA Conference + Expo, go here. And mark your calendars for the 2026 EFA Conference + Expo, to be held March 16-18, 2026, in Phoenix. For more information, visit environmentsforaging.com.